Patent and Non-Patent Search & Analysis
Customized services for technology landscaping, patentability assessment, freedom-to-operate, infringement, and invalidity searches and more.
Why us?
- Technical subject matter knowledge
- Search & database experience
- Deep Web non-patent search tools
Technology Trends & Competitor Analysis
Comprehensive analysis of patents, technical literature, product materials, and online sources to identify white spaces, monitor competitors, scout potential partners, and uncover strategic insights.
Why us?
- Connect-the-dots experience
- Big data tools to aid human analysis
- Primary research support
Patent Drafting, Filing & Prosecution Support
Patent drafting & prosecution services provided by U.S. and Indian patent agents aided by technical subject matter experts with many years of experience.
Why us?
- Working alongside inventors
- Proven prosecution success
- Patent litigation experience
Online Knowledge Management Portals
An internal IT team with many years of experience in designing user-friendly and intuitive portals.
Reports are available in online portals
Why us?
- Receive data updates seamlessly
- Share hassle-free report access
- Flexible, in-depth analysis
Training Services
We offer web-based and in-person training for R&D and IP professionals. Our sessions are interactive with many live exercises.
Why us?
- Trainers are IP specialists
- Extensive live exercises
- Hands-on project mentoring
Our company
Your knowledge partner of choice
Discover our company
Learn more about us.
Why choose us
Here are 3 reasons why you should choose us
Technology & Partners
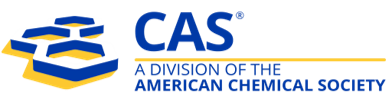
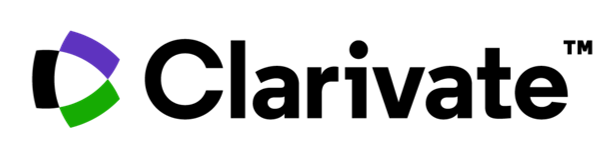
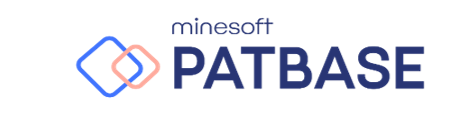
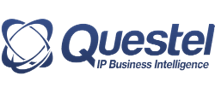
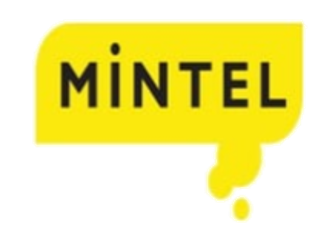
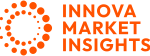
our approach
How we meet your need
Many thanks to you and the team for the results presentation yesterday, it was most informative. It is great to know your team’s thoughts from the analyses.
I just want to give you a heads-up that our European attorney was very impressed with the search results and analysis and I have given to her your name along with a strong recommendation for the quality of your work.
Thank you for sharing the great news, really our whole Research team is feeling very proud of this moment. Thank you so much for your support for achieving this important mile stone for us.
Excellent work and I am extremely encouraged by what SPA have found so far.
Invalidation records and arguments were very well done in Patent Art.
SPA has really dug through a lot of information & done an excellent job.
Patent Art provided very comprehensive and valuable insights.
Thank you for your email this makes me feel very comfortable with the approach your firm takes with the FTO projects we send to you. This is very helpful. So, your approach is spot on and the right way to go!
Congratulations to ‘team SciTech’ for all the support. There is no doubt that this (or US patents) would not have come through without your constant follow-up.
顧客の要望に沿った柔軟な対応能力、多様な分析手法の活用及び提案 能力」(国内化学大手)
「品質の高さに加え、企画提案能力が魅力的」(国内FA大手)